Galvanisation of Iron: Protecting Iron with Zinc and the Legacy of Galvanism
Galvanisation of iron is a method of protecting iron galvanically from rusting and corrosion with application a coating of zinc. This technique is widely used in construction, infrastructures. Iron, despite its strength and versatility, is highly susceptible to rust when exposed to air & moisture. A zinc coating serves as a protective shield, safeguarding the metal from oxidizing and structural decay.
Why Galvanisation of Iron Is Essential Today
Iron reacts quickly with oxygen and water, forming iron oxide—commonly known as rust. This rust weakens iron over time, compromising its structural integrity. To counter this, galvanisation provides a preventive barrier, increasing the lifespan and reliability of iron components for example galvanised planters.
Galvanised definition and Its Link to Galvanism
The term “galvanization” is inspired by the 18th-century work of Luigi Galvani, whose discovery of galvanism—the generation of electricity through chemical reactions—laid the groundwork for various electrochemical galvanization process, including protective metal coatings.
While galvanization of iron is not the same as galvanism, it borrows the name due to its reliance on chemical activity between zinc and iron. Galvanize definition refers to the process of applying a zinc coating to iron or steel to protect it from corrosion.
This coating not only forms a physical shield but also provides sacrificial protection—zinc corrodes in place of iron, even if the surface is scratched or damaged.
Zinc Coating and Its Protective Role
Zinc is more chemically reactive than iron. When exposed to the environment, it oxidizes before the underlying metal does. This sacrificial behavior is an example of cathodic protection, where the zinc sacrifices itself to shield the iron from corrosion. Over time, zinc forms a passive zinc oxide layer, which enhances its durability and continues to block moisture and oxygen from reaching the metal underneath.
Limitations of Galvanized Iron
While galvanisation of iron significantly improves its corrosion resistance, it has certain limitations that make it unsuitable for some environments and applications:
High-Temperature Conditions
Galvanized coatings begin to degrade at temperatures above 200°C (392°F), and lose effectiveness completely around 500°C (932°F). As a result, galvanized iron is not suitable for use in high-heat environments like furnaces, exhaust systems, or engine parts.
Acidic and Alkaline Environments
Zinc is reactive with both strong acids and bases. In settings such as chemical plants or facilities handling caustic substances, galvanized coatings may corrode rapidly, exposing the iron beneath.
Marine and Coastal Areas
Although galvanisation of iron can handle occasional salt exposure, it is not ideal for constant contact with saltwater, especially in splash zones. Prolonged exposure to seawater accelerates zinc corrosion, reducing the lifespan of the coating.
Architectural and Decorative Uses
Galvanized surfaces typically have a matte gray finish, which may not suit projects requiring aesthetic appeal. For decorative purposes, painted or powder-coated alternatives are often preferred.
Complex Shapes and Internal Spaces
Galvanizing objects with intricate designs or hollow interiors can be problematic. Uniform zinc coverage might not be achieved in tight or enclosed areas, leaving portions unprotected.
Welding Challenges
Welding galvanized iron emits hazardous zinc fumes and requires special precautions. The zinc must be removed before welding, which adds labor, cost, and safety concerns to the fabrication process.
Maintenance and Inspection
Even though galvanized iron is designed for low-maintenance use, regular inspections are recommended—especially in harsh environments. If damage or exposure occurs, touch-up with zinc-rich paints or sprays helps restore the protective layer. Periodic maintenance ensures the coating continues to protect the iron beneath.
Conclusion
Galvanisation of iron is a time-tested solution for corrosion protection, especially in construction, outdoor structures, and infrastructure projects. The concept of galvanism, which inspired the term, connects the chemical reactivity of zinc with early discoveries in electricity and chemistry. Though the two are separate concepts, the influence of galvanism underlines the scientific basis for galvanisation of iron metals
However, it is crucial to understand the galvanisation of iron has some limitations. High temperatures, corrosive chemicals, and continuous saltwater exposure can degrade galvanized coatings. Moreover, its appearance and welding challenges may not align with all design or industrial needs.
When selecting materials for a project, understanding both the advantages and drawbacks of galvanized iron ensures that the right protective solution is chosen. This balance of function, safety, and longevity supports efficient engineering and cost-effective infrastructure development over time.
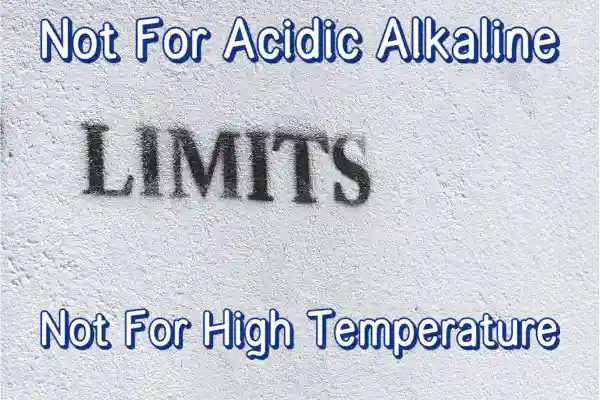